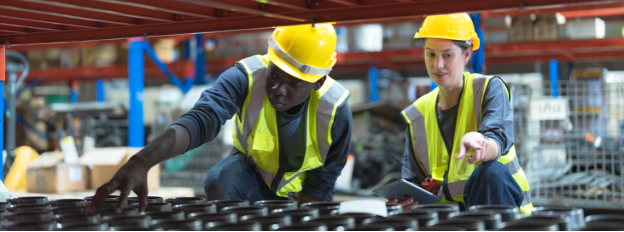
Top Supply Chain Management Solutions to Implement in 2024
When it comes to supply chain management, 2024 is introducing a spectrum of cutting-edge solutions aimed at simplifying operations, boosting efficiency, and addressing new challenges. Let’s explore six different supply chain solutions and the role of integrated supply chain management in navigating these advancements.
6 Supply Chain Solutions for 2024
Integrated supply chain management involves the seamless coordination of various supply chain functions. It ensures that different elements — from procurement to distribution — work in harmony. So, consider integrating the following supply management solutions into your 2024 business plan.
1. Computerized Maintenance Management System (CMMS)
CMMS is a digital solution that revolutionizes maintenance processes. By automating maintenance scheduling, tracking equipment performance, and managing work orders, CMMS ensures optimal equipment functionality. This proactive approach minimizes downtime, reduces costs, and extends the lifespan of critical assets.
Tips for Getting Started
- Regular Training: Ensure your team is well-trained in utilizing the CMMS. Regular training sessions can enhance their proficiency and maximize the system’s potential.
- Integration with IoT: Explore integration possibilities with IoT devices to enable real-time data collection. This enhances the accuracy of condition monitoring and predictive maintenance.
- Customized Reporting: Tailor CMMS reports to align with your specific business goals. Customized reports provide insights that are directly relevant to your organization’s unique needs.
2. Vendor Managed Inventory (VMI)
VMI shifts inventory management responsibilities to suppliers, allowing them to monitor stock levels and replenish products as needed. This collaborative approach reduces stockouts, excess inventory, and carrying costs. Vendor-managed inventory fosters efficient communication and collaboration between suppliers and organizations, leading to a more synchronized supply chain.
Tips for Getting Started
- Performance Metrics: Establish key performance indicators (KPIs) for VMI effectiveness. Regularly assess supplier performance against these metrics to ensure alignment with supply chain goals.
- Collaborative Planning: Collaborate with suppliers on demand planning and inventory strategies. Shared forecasting and planning contribute to a more synchronized and efficient supply chain.
- Technology Integration: Leverage technology for seamless communication. Implement automated systems that allow for real-time data exchange between your inventory management system and suppliers’ systems.
3. Industrial Vending
Industrial vending machines provide a self-service approach to managing consumables and tools. These machines offer real-time tracking, control access to high-value items, and streamline procurement processes. Industrial vending solutions enhance visibility, reduce wastage, and promote cost-effective supply chain inventory management.
Tips for Getting Started
- Strategic Placement: Strategically place vending machines at locations with high traffic and demand. Analyze usage patterns to determine the optimal placement of vending solutions within your facilities.
- User Training: Train employees on how to use industrial vending machines. Familiarity with the system encourages proper utilization and reduces the risk of errors.
- Regular Maintenance: Schedule routine maintenance for vending machines to prevent malfunctions. Regular checks and prompt repairs ensure uninterrupted access to critical supplies.
4. Remote Storeroom Management
Remote storeroom management involves the centralized oversight of multiple storerooms. With real-time visibility into inventory levels, usage patterns, and procurement needs, organizations can optimize stocking levels, reduce lead times, and ensure the timely availability of critical supplies.
Tips for Getting Started
- Centralized Oversight: Designate a central team responsible for overseeing storeroom management software. This team should have access to real-time data to make informed decisions.
- Regular Audits: Conduct regular audits of remote storerooms. These audits ensure accuracy in inventory records, prevent discrepancies, and identify opportunities for improvement.
- Technology Integration: Leverage technology to bridge the gap between remote storerooms and central oversight. Utilize cloud-based solutions for real-time data access and communication.
5. Condition Monitoring
Remote condition monitoring utilizes sensor technology to track equipment performance in real time. By detecting potential issues before they escalate, organizations can proactively schedule maintenance, prevent unexpected breakdowns, and extend the life of assets. This predictive approach improves overall equipment effectiveness.
Tips for Getting Started
- Comprehensive Sensor Deployment: Ensure comprehensive deployment of sensors on critical equipment. Cover various parameters to enable a holistic view of equipment condition.
- Predictive Maintenance Planning: Use condition monitoring data for predictive maintenance planning. This approach minimizes downtime and extends the life of equipment.
- Continuous Calibration: Regularly calibrate sensors to maintain accuracy. Continuous calibration ensures that condition monitoring data remains reliable for decision-making.
6. MRO Procurement Analytics & Data Enhancement
Analyzing procurement data optimizes the maintenance, repair, and operations (MRO) process. Advanced analytics and data enhancement tools provide insights into spending patterns, supplier performance, and inventory management. This data-driven approach enables informed decision-making, cost reduction, and process optimization.
Tips for Getting Started
- Unified Data Sources: Integrate data from various procurement sources into a unified platform. This provides a consolidated view — making it easier to analyze and improve procurement strategies.
- Regular Data Cleansing: Implement regular data cleansing processes. Clean, accurate data is essential for effective analytics and decision-making.
- Benchmarking Against Industry Standards: Benchmark procurement performance against industry standards. Identify areas where your organization can improve based on industry benchmarks.
Elevate Your Supply Chain in 2024 with DXP
At DXP, we understand the significance of integrated supply chain management. Explore our comprehensive supply chain services to optimize your operations, enhance efficiency, and stay ahead in the dynamic business landscape.
Contact a specialist today to learn more about DXP’s supply chain services.