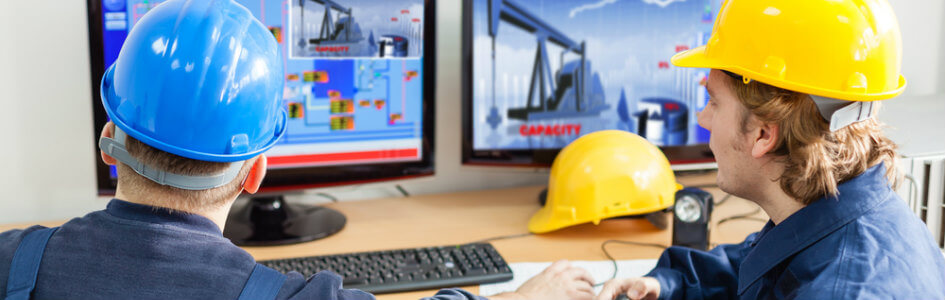
Using Vibration Analysis of Rotating Equipment to Diagnose Common Problems
Data-driven analytical systems are transforming the way rotating equipment, like industrial centrifugal pumps or air compressors, is monitored and maintained. Highly tuned temperature and vibration sensors placed at strategic points around a rotating equipment system can provide deep insights into potential equipment performance and alert operators to faults much more quickly than conventional methods, reducing downtime, improving energy efficiency, and extending the life of machinery.
Common Problems Uncovered by Rotating Machinery Vibration Analysis
Sensor systems can detect a range of common problems, including the following:
Misalignment
Alignment problems can cause significant wear and tear on a unit. Once a rotor is misaligned, it generates a radial force that is transferred to the rotor assembly, in many cases causing the misalignment to grow worse over time.
Left uncorrected, vibrations and temperature excursion caused by misalignment can lead to other issues, like failing seals, couplings, and bearings. Fortunately, shaft vibration analysis can usually identify this problem before system failure.
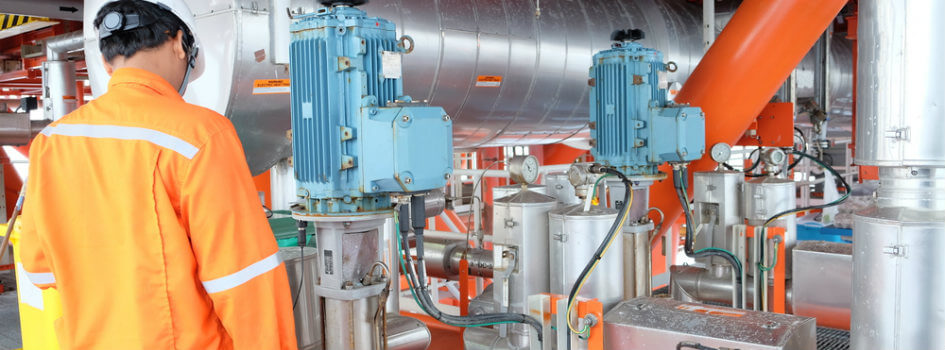
Unbalanced Operation
A loss of balance is a common problem in machines used in materials processing. When mass is not consistently distributed throughout the rotating mechanism, the point of greatest mass will vibrate. A sensor array used for machine vibration analysis can quickly detect the distinct, sinusoidal waveform of an unbalanced rotor’s vibration.
Loose Fittings
Rotating equipment should occasionally be visually inspected for parts that have become loose during operation. If a mounting bolt is loose, equipment can sometimes shift, causing low frequency vibrations.
Loose parts inside the rotor assembly can cause significantly worse problems, potentially creating imbalances or causing bearings to seize. Loose internal parts can cause a variety of vibrations and premature wear depending on their location and their interaction with other components. While vibration analysis methods will signal a problem in this case, it’s up to you to complete a visual inspection and resolve the root cause.
Fluid Instabilities
Many rotating equipment systems include the movement of fluids. If equipment is not precisely aligned and calibrated, internal fluids can cause specific types of vibrations. Such vibrations may be inconsistent and typically occur at an irregular frequency relative to rotor speed. Analyzing a system containing fluids requires careful consideration of the system’s components—seals, pumps, and compressors—that can affect fluid dynamics.
Worn-Out Parts
Bearings and other moving parts occasionally need to be replaced. From time to time, a part will begin to fail before its expected replacement date. Rotating machinery vibration analysis can detect the early degradation of parts as they introduce slip, friction or imbalances in a system.
Trust DXP with Your Rotating Equipment Needs
As a rotating equipment supplier and service provider, DXP provides a comprehensive suite of rotating equipment maintenance and monitoring services to customers in a wide variety of industries. For example, check out Predict-Plus™, our remote pump monitoring system, today!
Our experienced team of professionals can help your operation lower costs and improve equipment performance.
To learn more, give us a call at 1-800-830-DXPE or visit our website at www.dxpe.com!